Trimmed multilayered patches
Characterization and optimization of trimmed multilayered patches in the cavity passenger of public transportation vehicles
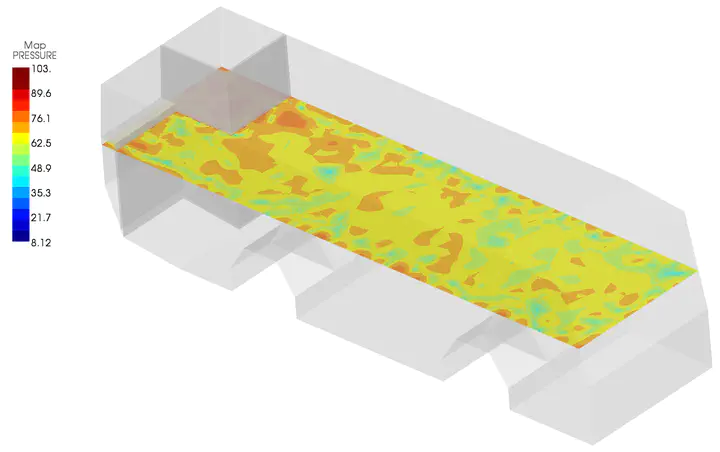
The aim of this joint project with a Spanish bus manufacturer consists in the development of novel green technologies to increase the acoustical comfort of the public transportation passengers (see reference [2]). More precisely, the optimal design of new coating materials for the interior vehicle have been suggested by means of their numerical characterization. Since most of the industrial suppliers for absorbing trimmed patches characterized their acoustic behavior by using international standards, for instance, ISO-10534, and such standards involves experimental measurements using a Kundt's tube, which can be mathematically modeled by a normal plane-wave analysis, the experimental data has been used to fit the physical coefficients in the non-linear frequency response mathematical models.
In fact, to determine the mechanical impedance associated to these patches or to deduce the frequency behavior of new multilayered patches with arbitrary thickness, it has been assumed: a) patches are local reacting panels and b) their time-harmonic motion of the foam layers are governed by the Allard-Champoux rigid-frame fibrous model and those micro-perforated layers are described by the Maa's impedance formula (see reference [1] for further details). In this model, the dynamic mass density and the dynamic bulk modulus depends on the frequency and the flow resistivity of the material. The computation of the last coefficient is obtained by solving an optimization problem to fit the experimental data in a wide frequency range (see Figure 1).
Figure 1: Experimental data and fit values of the imaginary
part of the mechanical impedance associated to a coating patch.
Since the novel multilayered absorbing patches are composed by combining micro-perforated plates, porous layers and inner air cavities, these new configurations must be optimized by analyzing the plane-wave absorbing coefficients optimizing its geometrical configuration and the material composition in each layer. Once, the final optimal design for the multilayered coating is computed, the values of the mechanical impedances can be included in a standard finite element formulation of the three-dimensional structural-acoustic problem. This methodology is illustrated in the numerical simulation of a passive control noise implemented in a bus (see Figure on the top of the page).
References
[1] A. Bermúdez, P. Gamallo, L. Hervella-Nieto, A. Prieto.Numerical simulation of active-passive cells with microperforated plates or porous veils.
Journal of Sound and Vibrations, 329 (2010), 3233-3246.
[2]
A. Bermúdez, F. J. González Diéguez, A. Prieto.
Characterization and optimization of trimmed models in passive control noise problems.
Poster at Mathematics for Innovation: Large and Complex Systems, Tokyo, 28 February-4 March (2012).